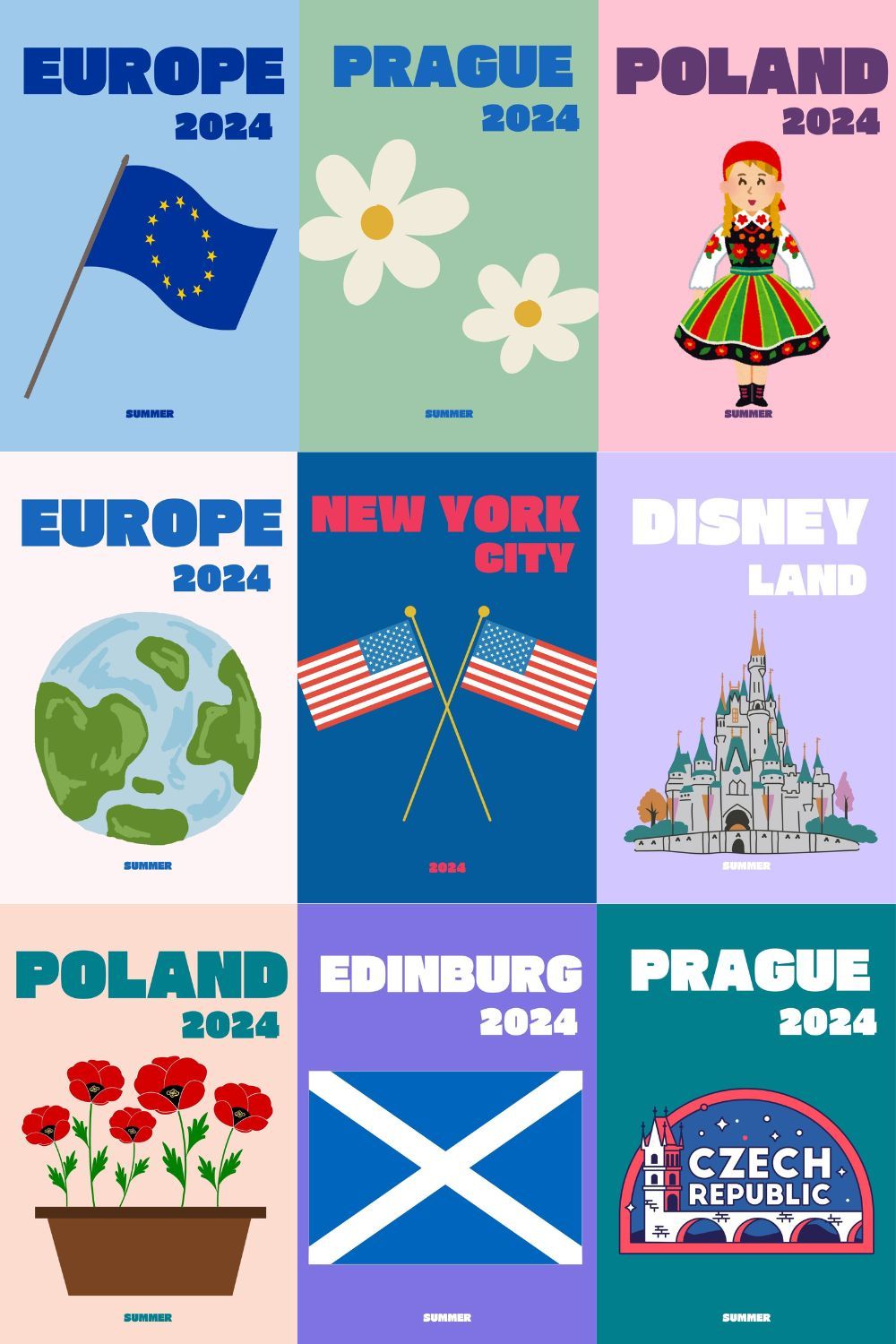
Arconic's Advanced Materials Power Volvo's Seamless Gear Shifts
PITTSBURGH, PA – October 26, 2023 – You might not think much about it when you're cruising in your Volvo, but that smooth, satisfying click as you shift gears? A lot of that comes down to materials science, and increasingly, that means Arconic. Arconic US LLC, a leading manufacturer of advanced materials headquartered in Pittsburgh, Pennsylvania, is quietly becoming a crucial partner to automotive giants like Volvo, providing the specialized aluminum alloys that underpin key components – including the gear shift mechanism. For years, Volvo has been synonymous with safety, quality, and increasingly, a sophisticated driving experience. That experience isn’t just about horsepower or design – it's about the little things. Things like how solid and precise the gear shift feels. And that’s where Arconic steps in. “We’re not designing the gear shift,” explains Sarah Miller, a materials engineer at Arconic’s Pittsburgh facility. “We’re supplying the high-performance aluminum alloy that allows Volvo’s engineers to create that perfect feel. It's about working with them to achieve their vision.” Beyond Just Metal: The Importance of Alloy Selection So what makes Arconic’s aluminum different? It's not just about being lightweight, although that’s a big plus for fuel efficiency. It’s about the specific composition of the alloy – a carefully controlled blend of aluminum with other elements like magnesium, silicon, and copper. “Think of it like baking a cake,” says David Chen, Arconic’s Automotive Account Manager. “You can use flour, sugar, and eggs, but the ratios and quality of those ingredients determine whether you get a fluffy masterpiece or a dense brick. We meticulously control the composition of our alloys to achieve specific properties.” For Volvo’s gear shift application, those properties are critical. The alloy needs to be: High Strength: The gear shift mechanism endures repeated stress and force. It needs to withstand those loads without bending, cracking, or failing. Arconic’s alloys are engineered for exceptional strength, ensuring longevity and reliability. Excellent Fatigue Resistance: This is huge. Fatigue resistance is the ability to withstand repeated cycles of stress. Imagine shifting gears hundreds of times a day, every day, for years. The alloy must resist cracking under that constant strain. Arconic’s proprietary alloy formulations significantly extend the lifespan of the gear shift components. Precise Dimensional Control: The gear shift mechanism is a complex assembly. Each component needs to be manufactured to incredibly tight tolerances. Arconic's advanced manufacturing processes ensure that the aluminum components meet Volvo’s exacting specifications. "We're talking about tolerances measured in thousandths of an inch," explains Miller. "It needs to fit perfectly." Good Machinability: The alloy needs to be easy to machine – to cut, drill, and shape – into the complex components of the gear shift mechanism. Arconic's alloys are specifically designed for efficient machining, reducing manufacturing costs and waste. Corrosion Resistance: Cars aren’t always driven in perfect conditions. The alloy needs to resist corrosion from salt, water, and other environmental factors, ensuring long-term durability. How Arconic Makes the Difference Arconic doesn't just sell aluminum; they engineer solutions. The company’s process involves a close collaboration with Volvo’s engineering team. “We work with Volvo from the very beginning of the design process,” says Chen. “We understand their performance requirements, and we tailor our alloys to meet those needs. It’s not a ‘one-size-fits-all’ approach.” The process typically involves: 1. Material Selection: Based on Volvo’s requirements, Arconic’s materials scientists identify the most suitable alloy composition. 2. Alloy Development: Arconic can even customize existing alloys or develop entirely new formulations to achieve specific performance characteristics. 3. Casting & Extrusion: Arconic uses advanced casting and extrusion processes to create the aluminum components in the desired shapes and sizes. These processes are tightly controlled to ensure consistent quality and dimensional accuracy. 4. Machining & Finishing: The components are then machined to precise tolerances and finished to meet Volvo’s specifications. 5. Quality Control: Rigorous quality control checks are performed throughout the entire process to ensure that every component meets Arconic’s and Volvo’s standards. The Future of Automotive Materials Arconic isn't stopping at gear shifts. The company is actively developing new aluminum alloys and manufacturing processes to address the evolving needs of the automotive industry. “We’re seeing a huge push for lighter vehicles, which improves fuel efficiency and reduces emissions,” says Miller. “Aluminum is perfectly positioned to play a key role in this trend. We're also exploring new alloys that offer even greater strength, fatigue resistance, and corrosion resistance.” Arconic is also investing in sustainable manufacturing practices, reducing its carbon footprint and minimizing waste. “We’re committed to being a responsible supplier to the automotive industry,” says Chen. “That means not only providing high-quality materials but also doing so in an environmentally sustainable way.” So, the next time you’re enjoying the smooth, satisfying feel of your Volvo’s gear shift, remember that there’s a lot more going on under the surface than meets the eye. And a good portion of that precision and reliability comes courtesy of Arconic's advanced aluminum alloys. It’s a small part, perhaps, but a critical one, in delivering the driving experience Volvo’s customers expect.