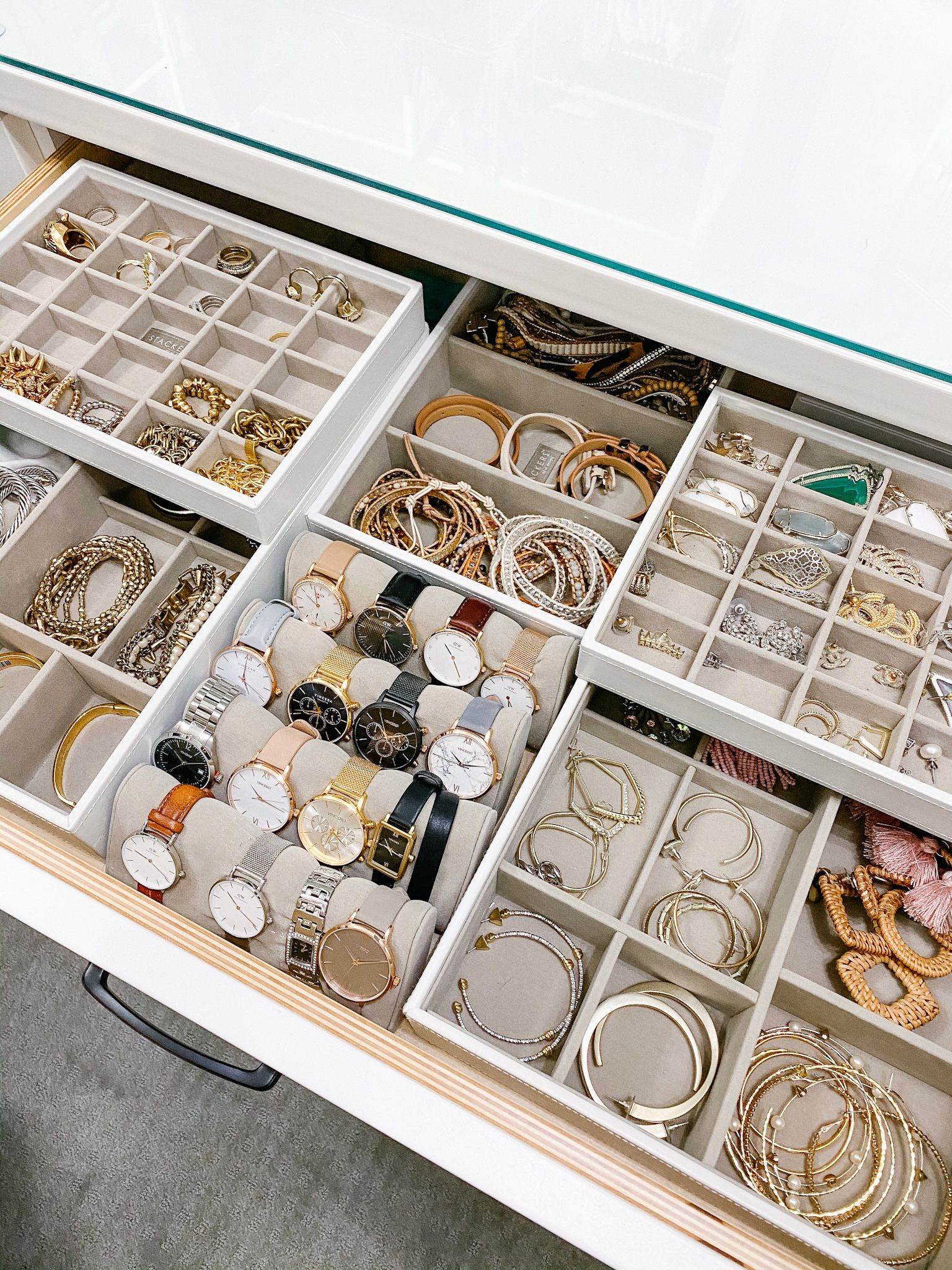
Arconic's Advanced Materials Power Smoother Shifts in New Volvo Models
Pittsburgh, PA – October 26, 2023 – Arconic US LLC, a world leader in advanced engineered materials, is quietly playing a critical role in enhancing the driving experience for Volvo drivers. While most eyes are on Volvo's sleek designs and safety features, it's the precision-engineered components inside the vehicle, like the gear shift mechanism, where Arconic's expertise shines. For years, Volvo has been a name synonymous with reliability and a smooth, comfortable ride. Now, with the latest generation of vehicles, they've upped the ante, and Arconic is a key partner in making it happen. We're talking about a significant upgrade to the gear shift – smoother, quieter, more precise, and built to last. So, what’s Arconic’s involvement? It's not a flashy exterior part you'll see, but a crucial internal component – high-performance aluminum alloys expertly crafted into the core structure of the Volvo gear shift mechanism. These aren’t your grandma’s aluminum parts. We're talking about alloys specifically designed to handle the stresses and strains of modern transmissions. “Volvo came to us looking for a material that could deliver exceptional strength, reduce weight, and improve the overall feel of the gear shifts,” explains a materials engineer at Arconic’s Pittsburgh headquarters. “They needed something that wouldn't just work, but would enhance the premium driving experience Volvo is known for.” Why Aluminum? Why Arconic? You might be wondering, why not just stick with steel? The answer is a multi-faceted one, and it highlights Arconic’s core strengths. First, weight. Aluminum is significantly lighter than steel. Reducing weight isn't just about fuel efficiency (though that’s a big part of it). Lighter components reduce the overall stress on the transmission, leading to improved durability and potentially longer component life. Second, vibration damping. Aluminum has natural vibration-damping properties, meaning it absorbs and dissipates energy, resulting in a quieter and smoother operation. No one wants a clunky, rattling gear shift! Third, precision manufacturing. This isn’t about just melting down aluminum and casting a part. Arconic specializes in advanced alloy development and precision manufacturing techniques. We’re talking about tight tolerances, complex geometries, and a relentless focus on quality control. The Volvo gear shift mechanism requires incredibly precise parts, and Arconic delivers. “The key is our ability to tailor the alloy composition and manufacturing process to meet Volvo’s exact specifications,” adds the engineer. “We don’t just sell aluminum; we provide material solutions.” Beyond Strength: Durability and Longevity Volvo isn't just focused on how the gear shift feels today; they're thinking about how it will perform years down the road. That’s where Arconic’s expertise in corrosion resistance comes into play. The aluminum alloys used in the Volvo gear shift are specifically formulated to withstand the harsh conditions inside a transmission – exposure to fluids, heat, and constant mechanical stress. “We’ve invested heavily in developing alloys that resist corrosion and maintain their structural integrity over time,” explains a metallurgist at Arconic. “Volvo demands reliability, and we’re committed to delivering it.” The Manufacturing Process: From Alloy to Component The journey from raw aluminum to a finished gear shift component is a complex one. Here's a simplified look at the process: 1. Alloy Selection: Arconic works closely with Volvo’s engineers to select the optimal aluminum alloy for the application. This involves considering factors like strength, weight, corrosion resistance, and manufacturability. 2. Casting/Forging: The selected alloy is then formed into a near-net-shape component using either casting or forging processes. Arconic utilizes state-of-the-art equipment and techniques to ensure the highest levels of precision and quality. 3. Machining: The cast or forged component is then precisely machined to meet Volvo’s exacting specifications. This involves removing excess material and creating intricate features and geometries. 4. Surface Treatment: The machined component undergoes a surface treatment process to enhance its corrosion resistance and improve its aesthetic appearance. 5. Quality Control: Throughout the entire manufacturing process, Arconic employs rigorous quality control measures to ensure that every component meets Volvo’s stringent requirements. This includes visual inspections, dimensional measurements, and destructive testing. A Partnership Built on Innovation The collaboration between Arconic and Volvo is more than just a supplier-customer relationship. It’s a partnership built on innovation, shared expertise, and a commitment to delivering exceptional products. “We work closely with Volvo’s engineers throughout the entire development process,” says a sales manager at Arconic. “We’re not just selling them parts; we’re providing them with material solutions that help them achieve their goals.” Arconic’s involvement in the Volvo gear shift mechanism is a testament to the power of advanced materials in enhancing the driving experience. While it may not be a visible component, it plays a crucial role in delivering the smooth, precise, and reliable performance that Volvo drivers expect. About Arconic: Arconic US LLC, headquartered at 201 Isabella Street, Pittsburgh, PA, 15212, United States (870-473-6666), is a leading provider of advanced engineered materials. We create innovative solutions for a wide range of industries, including aerospace, automotive, packaging, and construction. With a relentless focus on quality, innovation, and customer satisfaction, Arconic is committed to delivering solutions that make a difference. We don’t just make materials; we build possibilities.